You are here: Home > New Equipment > Aerial Lifts > Forklifts, Telescopic | |||||||||||||||||||||
Lull 644B-42 Forklift Telescopic 42' 6,000lbs.Operating Information
How a Forklift Works
If you drive a forklift on an incline, you must keep the load on the uphill side. Otherwise, you may have no weight on the wheels that steer and can lose control! The load could also fall off or cause the forklift to tip. Often a large forklift load obstructs the driver’s view in one direction. It may be necessary to travel long distances with the load to the rear (in reverse for most forklifts). Use extra caution when traveling in reverse. Forklift safety features A backrest extension on the forks prevents part of the load from falling rearward toward the operator. This is required when loads are lifted high and the type of load would allow all or part of it to fall to the rear under conditions such as acceleration, sudden stops or driving on an uneven surface. An overhead guard prevents an object on the forks or on a high rack from falling onto the operator while picking or placing a load at elevation. The guard is not designed to withstand the impact from a full load. It can be effective in deflecting small packages. It is required on all forklifts that can lift a load above the operator unless conditions such as clearances would not allow the forklift to be used. Operator restraints will hold you in the seat if you strike an object or if the forklift overturns. Since 1992, forklift manufacturers have been required to equip new forklifts with operator restraints such as seat belts. Many forklift manufacturers offer restraint systems that can be retrofitted on older forklifts. If your forklift begins to overturn, you are safest when you stay in the seat, hold on firmly, and lean in the opposite direction of the fall rather than trying to jump. Many fatal accidents happened when the operator tried to jump. As the forklift begins to tip, it will move slowly – tricking the operator into believing there is time to jump. Once the center of gravity is past the wheel line, the forklift will rapidly fall. The forklift’s overhead guard will quickly pin or crush an operator who jumps. Failure to wear a seat belt can result in the operator being thrown outside the protective cage in the event of overturn. If your forklift has a restraint such as a seat belt or a lap bar, you must use it. How forklifts safely carry and lift heavy loads A forklift works on the principle of a cantilever. A load on a beam (the forks) supported by a fulcrum (the front wheels) is counterbalanced by a weight on the other end of the beam (the forklift body and counterweight built into it). Whether a forklift will safely carry a load or will tip forward can be determined by comparing the "moment" of each. Moment equals the distance from the fulcrum to the center of gravity (the point where all the weight is concentrated) times the weight. Example: an evenly distributed 36" wide load on the forks has a center of gravity that is 18" from the face of the forks. (Note: The fulcrum point is actually at the center of the wheel. Forklift load charts, however, are adjusted to allow measuring from the face of the forks.) If the load weighs 4000 pounds then the load moment will be (18" x 4000 lb.) = 72,000 inch-pounds. If the "moment" of the forklift is greater than or equal to the 72,000 inch pounds of the load then the forklift will safely carry the load. Forklifts have a capacity plate to tell the user what loads are safe to lift. If the plate says the capacity is 30,000 pounds or less then that capacity is rated for a load with a center of gravity 24” from the face of the forks. If the forklift capacity is greater than 30,000 pounds then the label will rate the load at a 36" or 48" center of gravity since larger forklifts usually lift physically larger loads. For example, a forklift rated at 5000 pounds would safely lift a load with a moment of up to (24" X 5000 lb.) = 120,000 inch-pounds. In this case the load above would be safe to lift.
However if the 4000 pound load was 66" wide, the load moment would be (33" X 4000 lb.) = 132,000 inch-pounds which would be greater than the moment of the forklift. The forklift would tip forward. As the load is raised, it becomes possible for the forklift to fall to the side as well as tip forward. The operator must consider the center of gravity of the forklift and load together. This combined center of gravity moves as the load is moved and as the forklift travels over surfaces that are rough or inclined. Forklifts have a "stability triangle". The sides of the triangle as shown in the illustration are formed by the center of each front wheel and the center of the rear wheel or at the center of the axle if there are two rear wheels. A vertical line extending from the center of gravity of the vehicle-load combination must be inside of the stability triangle to prevent the forklift from tipping forward, falling sideways or dropping its load. The center of gravity of the forklift-load combination can move outside the stability triangle if:
These actions will have the following effects:
This list represents operator procedures that reduce the risk of overturn, collision or loss of the load. To prevent your forklift from tipping over, falling sideways or dropping its load:
|
We know your business success depends on reliable quality equipment and parts to continue being a leader in your industry. When you want Genuine Lull original equipment parts, accessories and equipment you can always depend on Discount-Equipment.com to come through with the genuine o.e.m. products you need as quickly and inexpensive as possible. Our sales staff combined experience consists of over 90 years in the construction parts and equipment industry. We have over 1 million items online, if you are having trouble finding your item, we also have the resources to help you find what you need, our industry leading web site includes thousands of parts and service manuals available to look up your items. If you don't find what you are looking for please fill out our parts request form here.
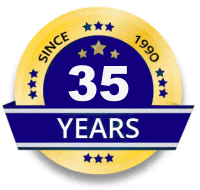